The automotive industry is rapidly evolving, driven by the demand for faster production, superior quality, and greater flexibility. Among the most impactful innovations in recent years is the laser coil cutting line—an integrated solution that combines decoiling, leveling, feeding, cutting, and unloading of sheet metal coils. This advanced technology is transforming automotive manufacturing by improving material utilization, accelerating changeovers, and enabling greater design versatility.
I. What is a laser coil cutting line?
A laser coil cutting line is a fully-automated system that deals with sheet coils by using its decoiler, leveler, feeder, laser cutter and unloading devices. Unlike mechanical blanking presses, which require hard tooling (dies) to punch out shapes, laser blanking is tool-free, meaning it uses software-driven laser beams to define the cutting geometry.
laser coil cutting lines typically include:
- Coil handling and decoiling devices
- Single- or multiple-head levelers or straighteners
- Laser cutting machines with multiple laser cutting heads
- Automated stacking systems like robots
- Integrated control and monitoring software
Combining decoiling, leveling, feeding, cutting and unloading together, the blanking line has developed into a one-stop production line from mere cutting and a sharp weapon to cut most sheet coils.
Generally speaking, laser coil cutting line is equipped with common laser cutting machine, but, SENFENG can accept customization of two decoilers, two, three or four crossbeams & laser cutting heads, in this way, sheet leveling and cutting speed is greatly raised. As for real scenes, please see the following video.
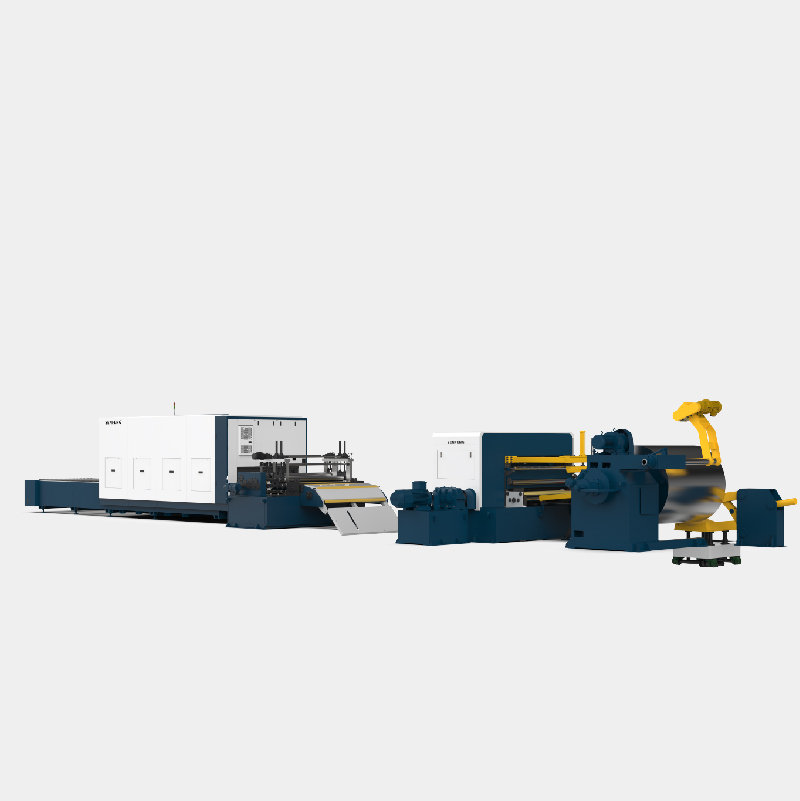
II. Why Automotive Industry Needs laser coil cutting lines
In general, the automotive industry faces several unique challenges:
- Frequent updates in design and model variations
- Lightweighting goals to improve fuel efficiency and EV range
- Much shorter development cycle
- Demands for higher flexibility in parts production
Traditional stamping lines struggle with these demands because of their dependency on heavy tooling, long changeover time and high costs for tool maintenance and storage. This is where laser coil cutting lines offer a transformative solution.
III. Key Benefits of laser coil cutting lines in Automotive Production
1. Tool-Free Operation and Design Flexibility
One of standout features of laser coil cutting line is its elimination of mechanical dies. All cutting paths are defined digitally, allowing manufacturers to adapt quickly to all changes with no need to fabricate or modify tooling. This offers several advantages:
- Faster prototyping and model launches
- Easy modifications of design
- Cost savings on die production and maintenance
For example, if a car manufacturer wants to change the geometry of door panel or body, engineers only need to update the digital files before starting production, with no downtime or tooling costs involved.
2. Higher Material Utilization (Nesting)
laser coil cutting lines allow for intelligent nesting, where parts shape is arranged digitally to maximize the used materials. However, traditional blanking dies require rectangular blanks with fixed dimensions, leading to more scraps.
With laser coil cutting lines, manufacturers can:
- Achieve higher material utilization (up to 10% savings)
- Reduce overall costs of raw materials
- Improve sustainability by lowering scrap rate
This is particularly valuable while dealing with expensive or lightweight materials such as aluminum and high-strength steels, which are widely used in modern vehicle structures.
3. High Precision and Clean Edge Quality
The laser cutting line delivers exceptional edge quality, producing burr-free and clean cuts that often eliminate the need for secondary processing. This is especially crucial in automotive manufacturing, where strict tolerances and structural integrity are essential.
Its high-precision cutting enhances downstream operations such as welding, forming, and assembly, helping to minimize defects and reduce rework throughout the production line.
4. Shorter Changeover and Setup Time
Since there is no physical tool to replace, changing from one part to another is nearly instantaneous. Changeovers can be done by simply loading a new cutting program into the system, allowing for:
- Flexible, on-demand production
- Easier batch or high-mix manufacturing
- Lower downtime and higher availability of the laser coil cutting line
This flexibility aligns with the automotive industry’s move towards modular platforms and personalized vehicle configurations.
5. Support for Lightweight Materials and EV Production
Electric vehicle (EV) makers are now placing heavy emphasis on reducing vehicle weight to prolong driving range. As a result, materials like aluminum, advanced high-strength steel (AHSS) and composites are increasingly used in body structures.
laser coil cutting lines are ideal for these materials, as they offer:
- Non-contact cutting that decreases stress and deformation
- Precision control over heat input
- Clean cutting of thin or sensitive materials
This makes laser coil cutting line a strategic helper for EV production lines and sustainable vehicle manufacturing.
IV. Applications of Laser Blanking in Automotive Manufacturing
laser coil cutting lines are widely used across various automotive sectors, such as:
- Body-in-white (BIW) panels: Like doors, hoods, roofs and fenders
- Structural reinforcements: Cross members, crash components and chassis parts
- Battery enclosures: Especially in electric vehicles
- Custom-made parts: Special editions, trims and prototypes
- Mixed-material assemblies: Multi-layer cutting or advanced nesting for composite parts
Because laser coil cutting line handles multiple types of materials and part geometries, it allows automakers to consolidate multiple stamping operations into a single flexible line.
V. Economic and Strategic Advantages
Although upfront costs of laser coil cutting lines are usually higher than other traditional press systems, the long-term ROI is attractive, especially for automakers that:
- Produce multiple vehicle models
- Handle frequent design changes
- Want to reduce inventory and storage of dies
- Aim for sustainability and material efficiency
laser coil cutting lines also reduce capital expenses related to tooling, shorten time-to-market, and lower operating costs through automation and improved throughput.
VI. The Future of Automotive Production
As the automotive industry transitions toward electric mobility, lightweight materials, and custom-made manufacturing, laser coil cutting lineis still developing into a key enabler of agility and innovation. With its unique combination of flexibility, precision and material efficiency, it helps automakers meet the demands of the modern users and global regulatory standards.
In the future, we may expect to witness even adoption of laser line technologies, especially as AI-powered optimization and adaptive laser controls, so as to further enhance cutting performance and production scalability.
VII. Conclusion
Laser coil cutting lines are transforming the landscape of sheet metal processing in the automotive industry. With unmatched flexibility, accuracy, and efficiency, they meet the industry’s increasing demands for agile, high-quality, and sustainable manufacturing. For OEMs and Tier 1 suppliers striving to future-proof their operations, adopting laser coil cutting technology represents a forward-looking and strategic investment. Senfeng offers laser coil cutting lines in various working formats, capable of processing different types and thicknesses of sheet metal. If you’d like to learn more, feel free to contact us.